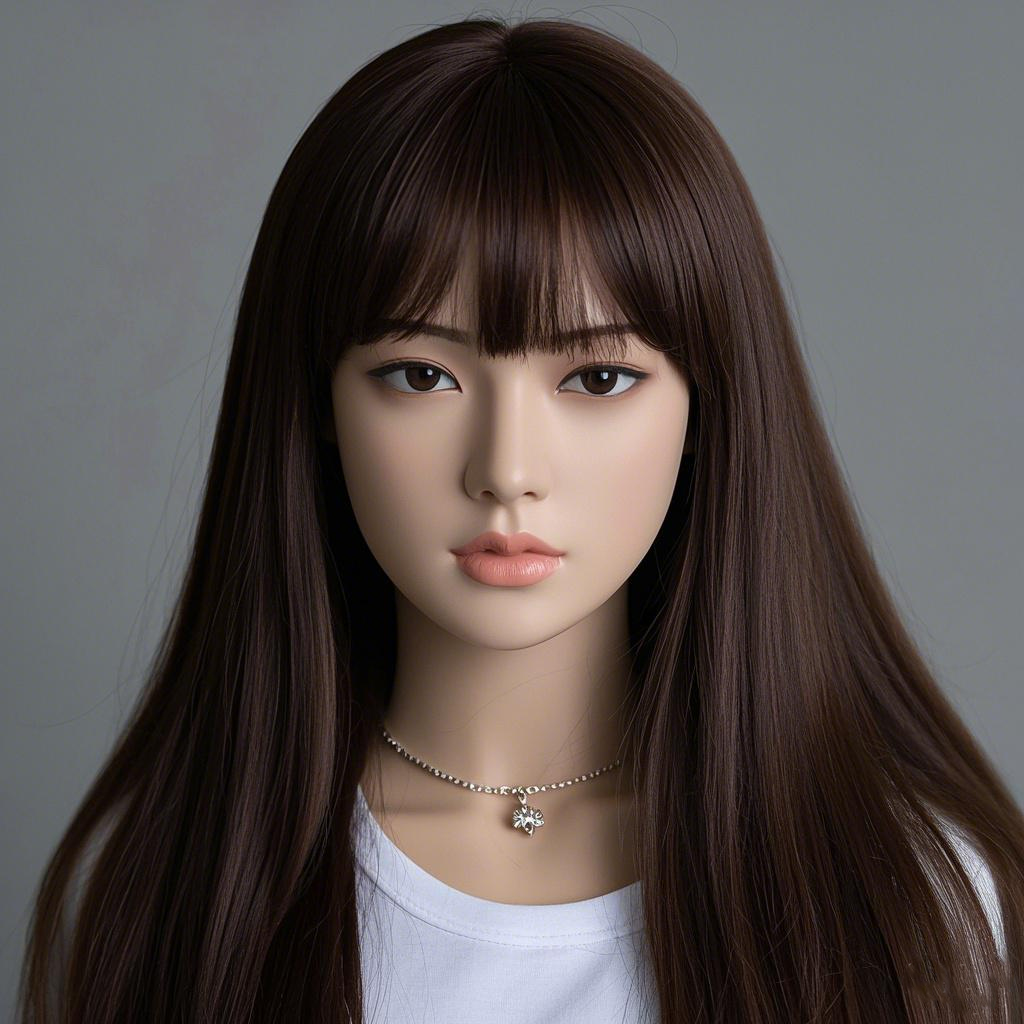
26
Feb
Kinky Straight Wig: The Fusion of Naturalness and Smoothnes
In recent years, the beauty industry has embraced technological advancements to improve production efficiency, product quality, and safety. One such product that has benefitted from automation is the kinky straight wig, a versatile hair product that replicates the natural texture of African-American hair. In this article, we explore how automation is transforming wig manufacturing, the role of lead safety barriers in ensuring a safe working environment, and the growing importance of quality control in the production process.
The Growth of the Wig Industry and the Role of Automation
The demand for wigs, particularly kinky straight wigs, has been rising due to their versatility, ease of use, and the growing popularity of protective hairstyles. As the demand grows, so does the need for efficient and safe production methods. This is where automation steps in, significantly reducing manual labor while ensuring consistent product quality.
Automation in the wig industry is not just limited to assembly lines. From hair fiber processing to final packaging, automated machines have streamlined the entire process. These machines ensure precision in every stage, from cutting hair strands to weaving them into perfect textures that mimic natural hair.
As automation technology advances in the beauty industry, it is crucial to maintain safety standards in the workplace. Lead safety barriers are a vital component in ensuring that workers are protected from potential hazards, especially in environments where machines are processing or handling materials that could be hazardous to human health.
In wig manufacturing facilities, automated machines like hair processing machines, weaving looms, and hair coloring systems are often used in tandem to increase efficiency. However, these machines can also pose safety risks if not properly safeguarded. This is where lead safety barriers come into play.
Lead safety barriers are essential for protecting workers from exposure to harmful substances, radiation, and physical dangers such as high-speed machinery and hot surfaces. In environments where chemicals are used for hair treatments or in areas with high-temperature machines, lead safety barriers help create a controlled environment by shielding workers from these hazards.
Automation and Quality Control in Kinky Straight Wig Production
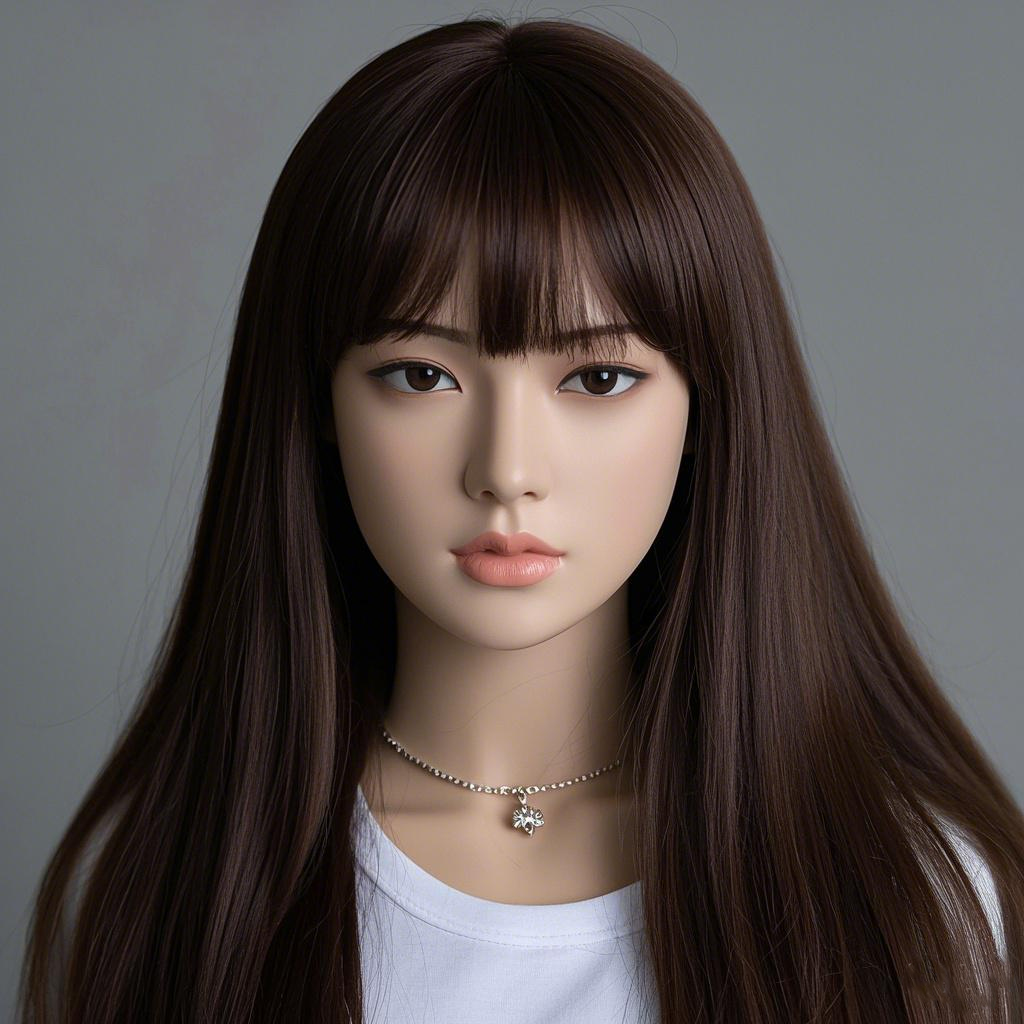
Automation also plays a significant role in quality control, ensuring that each kinky straight wig meets specific industry standards. Automated systems equipped with sensors and cameras monitor the production process, inspecting every wig for consistency in color, texture, and finish. This reduces human error and ensures that the final product meets customer expectations.
In addition to physical safety, the rise of automated quality control systems in wig manufacturing also reduces the risks associated with manual labor. These systems help prevent product defects and ensure that kinky straight wigs are produced with the highest standards in mind.
Conclusion
The beauty industry is witnessing a revolution in manufacturing, thanks to the introduction of automation. From improving efficiency to ensuring safety and enhancing quality control, automated systems are transforming the way kinky straight wigs are produced. And with the incorporation of lead safety barriers, the industry can continue to innovate while prioritizing worker safety. In the coming years, we can expect even more advanced automation solutions that will further elevate the quality, safety, and sustainability of wig production.
The Necessity of Safety in Automation: Why Lead Safety Barriers Matter
As automation technology advances in the beauty industry, it is crucial to maintain safety standards in the workplace. Lead safety barriers are a vital component in ensuring that workers are protected from potential hazards, especially in environments where machines are processing or handling materials that could be hazardous to human health.
In wig manufacturing facilities, automated machines like hair processing machines, weaving looms, and hair coloring systems are often used in tandem to increase efficiency. However, these machines can also pose safety risks if not properly safeguarded. This is where lead safety barriers come into play.
Lead safety barriers are essential for protecting workers from exposure to harmful substances, radiation, and physical dangers such as high-speed machinery and hot surfaces. In environments where chemicals are used for hair treatments or in areas with high-temperature machines, lead safety barriers help create a controlled environment by shielding workers from these hazards.